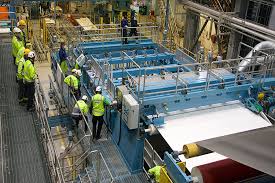
Safety is a combination of culture and attitude at UPM’s pulp mills in Finland. Each year, its Kymi, Kaukas and Pietarsaari mills produce impressive safety records across an industry with accident potential.With defined common rules and standards, along with a global safety management system used to share daily observations and learnings from accidents, safety is no accident at UPM’s pulp mills in Finland.
While the company takes a systematic and preventative approach to safety at its production facilities around the world to provide efficient, safe and clean working environments for all of its employees, contractors and visitors, the main focus is on reducing all accidents. This is achieved by identifying and removing potential hazards before they cause accidents.
Charged with the responsibility of managing safety and its continuous development at UPM’s pulp mills in Finland, safety manager Aki Huomo is acutely aware of the scale of operations and the sheer number of people he oversees.
Safety is in the culture
Typical accidents at UPM’s Kaukas, Kymi and Pietarsaari mills aren’t what you might think. Slips and falls, especially during the slippery winter, and small cuts to fingers are the most common. But pulp mills also use chemicals on site that can lead to serious accidents if personnel do not pay close attention.
“The most challenging part is that these types of injuries are also strongly related to people’s mindsets, rather than a lack of safety equipment,” says Huomo.
Sometimes, people need to just stop and think before doing – behaving in a proactive way can help prevent these types of smaller accidents.
“Our mindset is that zero accidents are possible, but we’re not there yet. What we’ve achieved is great but we have to keep our focus on the future and keep improving,” says Huomo.
With challenging targets, the responsibility stretches beyond UPM’s line organisation. It is also integrated into the everyday working life of all personnel, from general managers to the newest mill employees, sub-contractors and visitors.
While the company takes a systematic and preventative approach to safety at its production facilities around the world to provide efficient, safe and clean working environments for all of its employees, contractors and visitors, the main focus is on reducing all accidents. This is achieved by identifying and removing potential hazards before they cause accidents.
Charged with the responsibility of managing safety and its continuous development at UPM’s pulp mills in Finland, safety manager Aki Huomo is acutely aware of the scale of operations and the sheer number of people he oversees.
Safety is in the culture
Typical accidents at UPM’s Kaukas, Kymi and Pietarsaari mills aren’t what you might think. Slips and falls, especially during the slippery winter, and small cuts to fingers are the most common. But pulp mills also use chemicals on site that can lead to serious accidents if personnel do not pay close attention.
“The most challenging part is that these types of injuries are also strongly related to people’s mindsets, rather than a lack of safety equipment,” says Huomo.
Sometimes, people need to just stop and think before doing – behaving in a proactive way can help prevent these types of smaller accidents.
“Our mindset is that zero accidents are possible, but we’re not there yet. What we’ve achieved is great but we have to keep our focus on the future and keep improving,” says Huomo.
With challenging targets, the responsibility stretches beyond UPM’s line organisation. It is also integrated into the everyday working life of all personnel, from general managers to the newest mill employees, sub-contractors and visitors.
“Nowadays, a large part of safety involves communications and trying to change people’s behaviour. The message, style and method of communication are very important.” For example, older workers may be more inclined to digest their safety information via paper format, while younger personnel may prefer digital formats.
“We are trying to create a safe place for our employees. In whatever actions we take, we must keep in mind that they are also supporting the development of our safety culture,” Huomo says.
It’s a case of the numbers adding up
There’s safety in the numbers of employees at UPM’s mills in Finland. With 1,000 UPMers and several hundred contractors at the mill sites, it’s easy to understand why UPM’s mills take a safety-first approach to their work.
All UPM personnel are charged with making safety observations on a daily basis. They are not only encouraged but required to identify and report any potential hazards so that each can be handled and corrected by UPM’s line organisation.
“The small choices that we make daily are the main thing that can lead us to better safety performance,” says Huomo.
It’s a simple numbers game: the more personnel on site, the more pairs of eyes available to identify, report and neutralise possible hazards.
“We are trying to create a safe place for our employees. In whatever actions we take, we must keep in mind that they are also supporting the development of our safety culture,” Huomo says.
It’s a case of the numbers adding up
There’s safety in the numbers of employees at UPM’s mills in Finland. With 1,000 UPMers and several hundred contractors at the mill sites, it’s easy to understand why UPM’s mills take a safety-first approach to their work.
All UPM personnel are charged with making safety observations on a daily basis. They are not only encouraged but required to identify and report any potential hazards so that each can be handled and corrected by UPM’s line organisation.
“The small choices that we make daily are the main thing that can lead us to better safety performance,” says Huomo.
It’s a simple numbers game: the more personnel on site, the more pairs of eyes available to identify, report and neutralise possible hazards.
Accolades a safe bet
Each year UPM holds safety awards, in which each business area selects a nominee before the winner is selected on a group-level. The nominations are based on the previous years’ safety performance and safety work.
This year, the Kaukas mill received the ‘best improver’ award, due to its excellent development in safety. In the past four years, their accident frequencies have decreased very quickly, while at the same time they are conducting excellent safety preventive work.
Kymi mill is once again in the ‘front runner club’ which shows that it has also undertaken systematic work in terms of onsite safety, while the Pietarsaari mill was also a club member previous year and highly likely to receive a safety award in the near future as well.
However, when it comes to safety, the work is never done. “Each and every day we have to earn our safety performance once again. It doesn’t matter how good we were last year or two years ago – it matters how we are performing today,” says Huomo.
UPM- FINLANDIA -08 Setiembre 2020
Each year UPM holds safety awards, in which each business area selects a nominee before the winner is selected on a group-level. The nominations are based on the previous years’ safety performance and safety work.
This year, the Kaukas mill received the ‘best improver’ award, due to its excellent development in safety. In the past four years, their accident frequencies have decreased very quickly, while at the same time they are conducting excellent safety preventive work.
Kymi mill is once again in the ‘front runner club’ which shows that it has also undertaken systematic work in terms of onsite safety, while the Pietarsaari mill was also a club member previous year and highly likely to receive a safety award in the near future as well.
However, when it comes to safety, the work is never done. “Each and every day we have to earn our safety performance once again. It doesn’t matter how good we were last year or two years ago – it matters how we are performing today,” says Huomo.
UPM- FINLANDIA -08 Setiembre 2020